Case Study – Cost reduction and capacity improvement at a sanitary product factory in China
TRANSFORMATION BY WAY OF WORKER ENGAGEMENT THAT INCREASED ANNUAL PROFIT BY 3 MILLION USD
This manufacturing case study will showcase how our CMC consultants achieved real results at this Chinese factory by way of:
- Assembly Lines Re-engineering — Working hand-in-hand with top management, and with the knowledge-based of having set-up hundreds of lean-style manufacturing lines, CMC was able to drive line re-organization that resulted in increased productivity and speed.
- Hands-on Training Programs for Managers and Operators — CMC worked with the existing management team and allowed staff to start generating valuable suggestions, and implementing change, through a 6-month training program. Training focused a a variety of topics which you will read about, including basic lean training, preventive maintenance, material control, 5S, standard work, quick changeovers and quality alerts, and so on.
- Development of KPIs — As part of this engagement CMC consultants taught the factory how to set up KPIs for both top-level and middle-management, and even teams of line-workers. This allowed the factory to continue to drive continuous improvement even after the engagement was finished.
Over this 12-months engagement the factory reduced its cost structure by 1.5 million USD a year. Assembly line re-engineering and improved quality (i.e. less rework) allowed the factory to reduce the number of production operators from 208 to 123. The streamlining of administrative and support processes resulted in 38 fewer indirect workers, and better inventory control resulted in massive savings.
On top of all this, the increased capacity meant the factory was able to accept new business, resulting in 1.5 million USD in additional profit.
To read this in-depth case study and learn what tools CMC consultants used, simply fill out the form to the right and click DOWNLOAD.
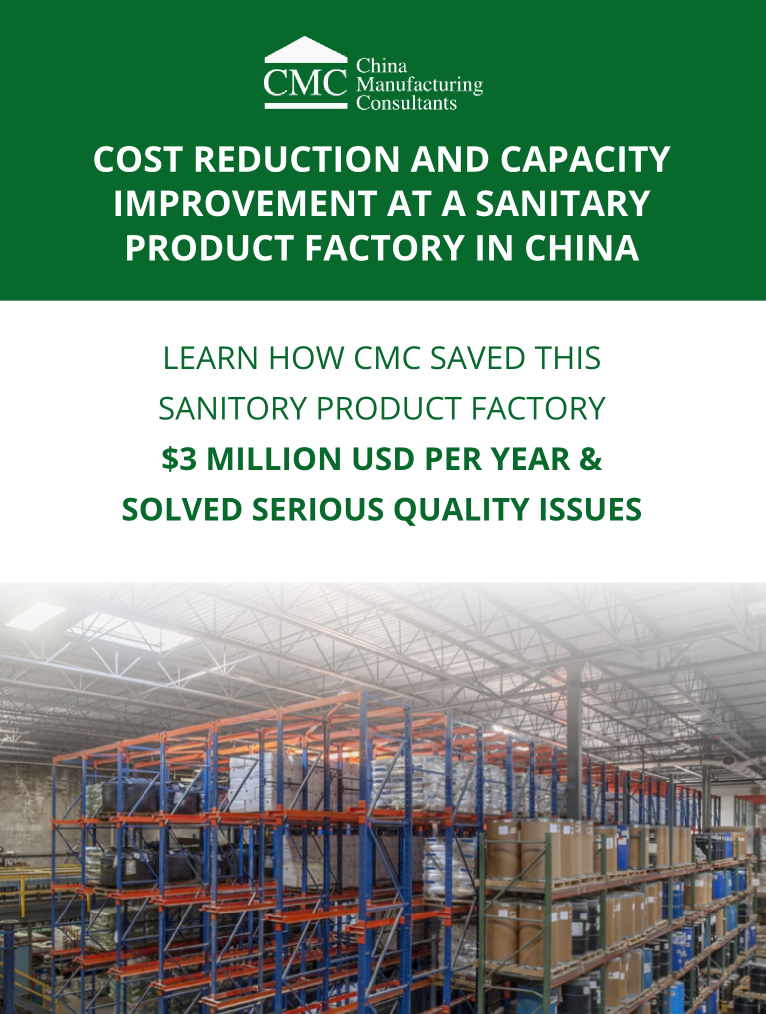