Case Study – Auto parts factory turn-around in China
HOW CMC HELPED AN AUTO PARTS FACTORY INCREASE PROFITABILITY AND CAPACITY BY 4X
Some key aspects of this manufacturing case study that you will read about include:
- Elimination of Bottlenecks – By taking the factory through a value stream mapping exercise, CMC consultants identified the bottlenecks and worked on elevating the factory’s capacity through process re-engineering.
- Production Planning — with CMC’s guidance the factory was able to switch to smaller batches, in order to reduce lead times, improve flexibility, and reduce inventory and transportation costs. CMC introduced a kanban system for machining and fabrication processes.
- Preventive Maintenance Plans — CMC showed the factory how to reduce the occurrence of machine breakdowns and the proportion of parts out of tolerance, thereby improving quality and capacity at the same time.
CMC allowed the factory to more than double the capacity of the existing factory in only 4 months, and then went on to 4X capacity. Then we increased the on-time shipment rate from 39% to 65%, and reduced monthly costs by 850,000 RMB through less rework, less scrap, higher productivity, and less delays. In addition, inventory levels decreased by nearly 5 million RMB, which meant the factory enjoyed a much stronger cash position.
To read this in-depth case study and learn what tools CMC consultants used, simply fill out the form to the right and click DOWNLOAD.
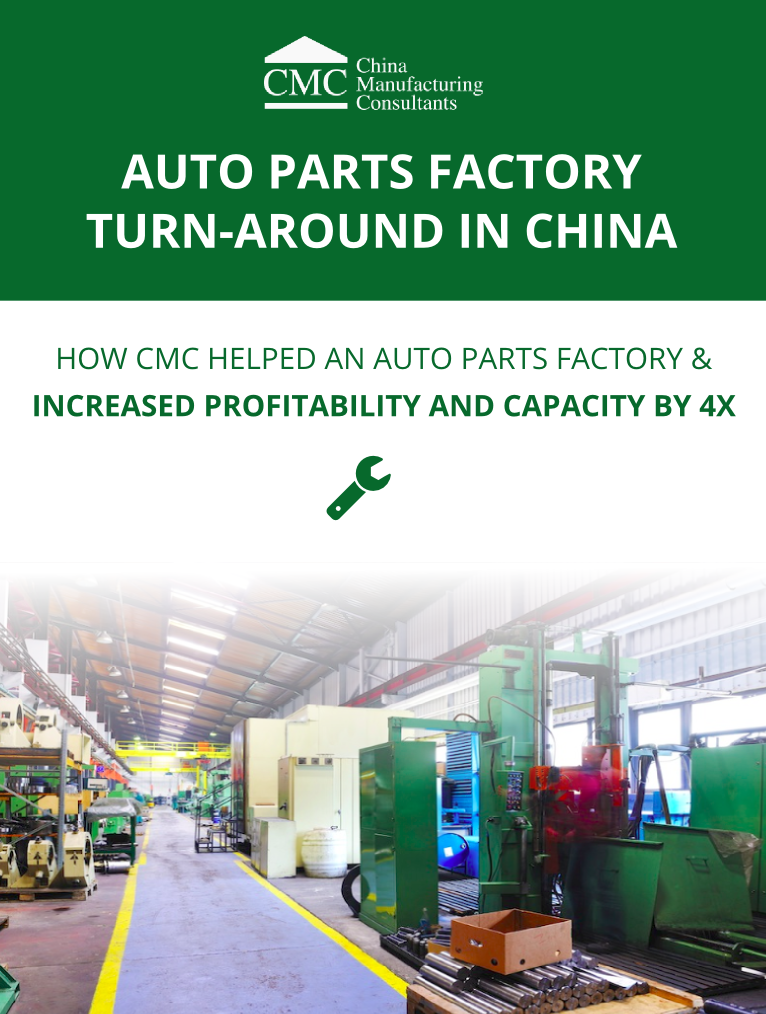